記事公開日
受託開発(ODM)の活用ケーススタディ10選
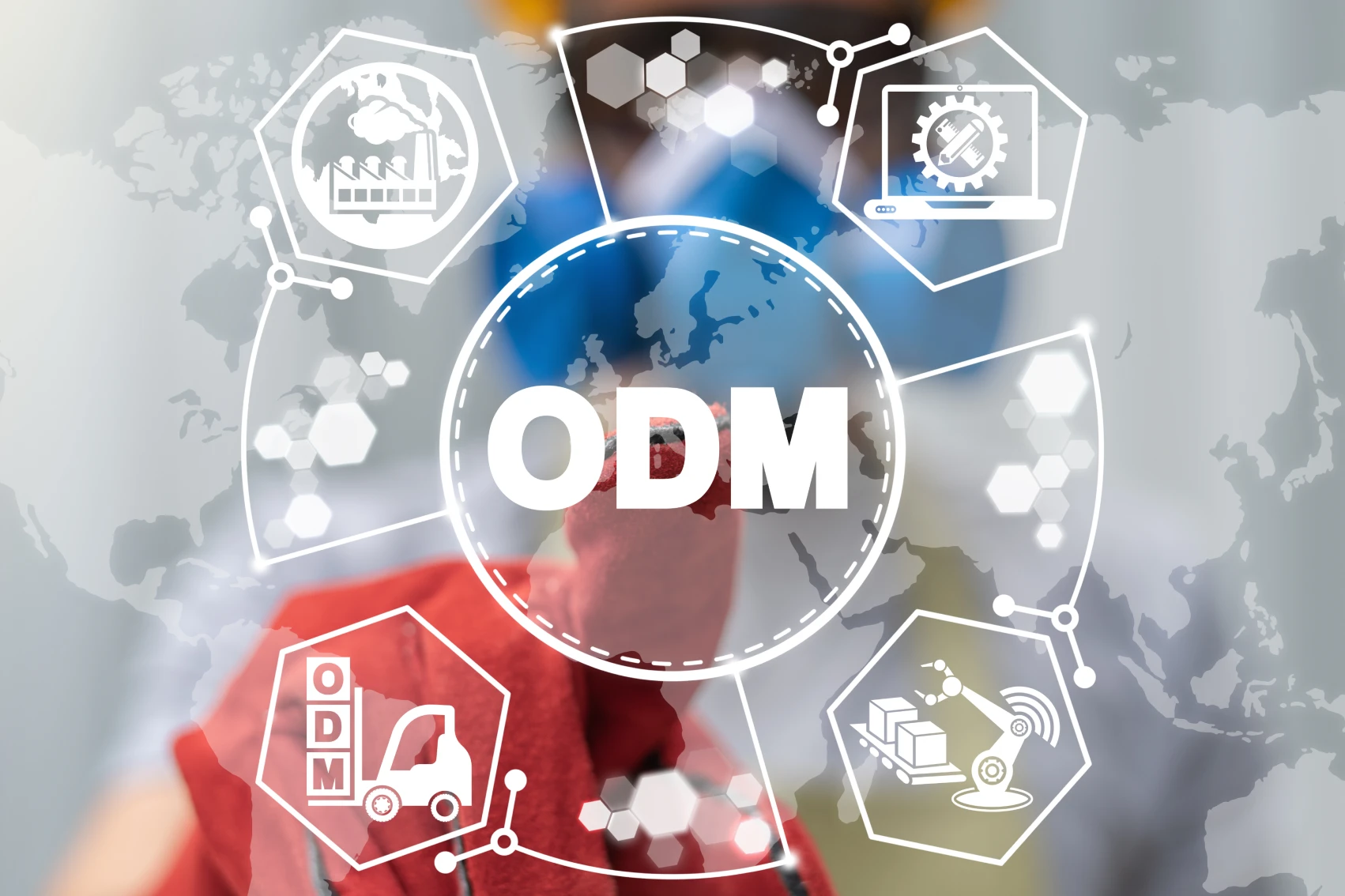
製造業において、自社ブランド製品の開発・生産を効率化し、競争力を強化する手段として 受託開発(ODM)の活用が注目されています。
ODMを活用することで、新規市場開拓やコスト削減、技術力向上など多様なメリットを享受できます。
近年、国内製造業では人手不足やコスト高騰の課題が深刻化し、ODMの導入による生産効率の向上や外部パートナーとの協業が求められています。
本記事では、ODMの活用ケーススタディを10点、ご紹介し、それぞれのケースでのポイントを解説します。ODMを戦略的に活用し、自社の成長を加速させるためのヒントを探っていきましょう。
- 【ケーススタディ1】化学業界:ODMを活用した新素材開発
- 【ケーススタディ2】医薬品業界:ジェネリック薬品のODM製造
- 【ケーススタディ3】食品業界:オーガニック食品ブランドのODM戦略
- 【ケーススタディ4】金属加工業界:特殊鋼のODM製造
- 【ケーススタディ5】電機業界:家電ブランドのODM活用
- 【ケーススタディ6】自動車業界:EV部品のODM製造
- 【ケーススタディ7】繊維業界:高機能繊維のODM
- 【ケーススタディ8】ゴム・プラスチック業界:耐熱素材のODM開発
- 【ケーススタディ9】医療機器業界:ODMによる高精度医療機器の製造
- 【ケーススタディ10】資源・エネルギー業界:環境対応製品のODM開発
- まとめ
【ケーススタディ1】化学業界:ODMを活用した新素材開発
近年、化学業界では環境規制の強化や市場ニーズの多様化が進み、企業は新素材開発のスピード向上とコスト削減の両立を求められています。
しかし、新素材の開発には高度な技術が必要であり、研究開発コストや設備投資が大きな負担となるケースが少なくありません。
そのため、多くの企業がODM(受託開発)を活用し、専門知識を持つ外部パートナーと協力して新素材開発を加速させる動きが広がっています。
課題
ある化学メーカーでは、電子部品の耐熱コーティング用途として、高耐熱性ポリマーの開発を計画しました。
しかし、以下の課題がありました。
■開発リソースの不足
新規素材の開発には特殊な設備と専門知識が必要であり、社内リソースでは対応が困難
■開発期間の短縮が必要
市場投入のスピードを上げるため、短期間での試作・量産化が求められる
■コスト負担の最適化
研究開発費や設備投資の負担を抑えつつ、高品質な製品を実現したい
このような状況の中、同社はODMパートナーを活用し、開発プロセスを最適化することを決定しました。
解決策
同社では、以下の流れでODMパートナーと協業し、効率的に新素材を開発しました。
1.ODM企業の選定
- 高耐熱性ポリマーの製造経験を持つ複数のODM企業をリストアップ
- 研究開発力・生産能力・品質管理の厳格さを比較し、最適なパートナーを決定
2.試作・評価
- 同社が要件定義を行い、ODM企業が試作品の開発・改良を実施
- 研究開発チームとODM企業が連携し、数十回の試作テストを実施
3.量産体制の確立
- ODM企業の生産設備を活用し、スケールアップ試験を実施
- 品質管理基準を確立し、大量生産が可能な体制を整備
4.市場投入
- ODM企業の協力により、開発期間を従来の約半分に短縮
- 競争力のある価格で新素材を市場投入
【ケーススタディ2】医薬品業界:ジェネリック薬品のODM製造
医薬品業界では、特許が切れた先発薬の代替品としてジェネリック医薬品の市場が拡大しています。
特に、高齢化社会が進む日本では、医療費削減の観点からもジェネリック医薬品の普及が推奨されています。
しかし、ジェネリック医薬品の開発には、GMP(Good Manufacturing Practice:適正製造基準)に準拠した高度な品質管理が求められるため、中小規模の製薬会社にとっては設備投資や生産コストの負担が大きく、参入のハードルが高いのが現状です。
このような課題を解決するために、ODM(受託開発)を活用することで、コストを抑えながら高品質なジェネリック薬品の製造が可能になります。
課題
ある製薬会社では、新たなジェネリック薬品の市場投入を計画していましたが、以下の課題を抱えていました。
■GMP認証取得の負担
自社でGMP基準に適合する工場を新設するには、多額の設備投資が必要
■生産コストの最適化
自社工場のラインを改修して量産体制を整えるのが困難
■市場投入のスピード向上
競争が激しい市場で、より早くジェネリック薬品を提供する必要がある
そこで、同社はODMを活用し、外部の専門製造企業と協力することで、ジェネリック薬品の開発・生産を効率化することを決定しました。
解決策
同社では、以下のステップでODM企業と協業し、ジェネリック薬品の市場投入を成功させました。
1.ODM企業の選定
- 医薬品製造に強みを持ち、GMP認証を取得しているODM企業をリストアップ
- 品質管理体制・生産能力・コスト競争力を評価し、最適なパートナーを選定
2.開発プロセスの共同管理
- Y社が開発した処方をもとに、ODM企業が試作と安定性試験を実施
- 効能・安全性を確認しながら、規制当局の認可を取得
3.量産体制の確立
- ODM企業の最新設備を活用し、大規模生産をスムーズに実施
- 品質検査とトレーサビリティ管理を徹底し、安定供給体制を確立
4.市場投入とブランド戦略
- ODM生産によるコスト削減分を活用し、競争力のある価格設定を実現
- 同社のブランドとして販売し、市場シェアを拡大
【ケーススタディ3】食品業界:オーガニック食品ブランドのODM戦略
近年、健康志向の高まりやサステナビリティへの関心の向上により、オーガニック食品市場が拡大しています。
特に、化学合成された農薬や添加物を使用しない「安全・安心な食品」へのニーズが高まり、多くの食品メーカーがオーガニック製品の開発に注力しています。
しかし、オーガニック食品の製造には、厳しい認証基準のクリア、原材料調達の難しさ、生産コストの高さなどの課題があり、自社のみでの生産には多大なコストと時間がかかります。
そのため、多くの企業がODM(受託開発)を活用し、専門の食品製造パートナーと協力してオーガニック食品の市場投入を加速させています。
課題
ある食品メーカーでは、健康志向の高まりを受け、オーガニックグラノーラの開発・販売を計画しました。
しかし、以下のような課題を抱えていました。
■オーガニック認証の取得が難しい
自社工場ではオーガニック認証(JAS認証)を取得しておらず、新たに認証を取得するには多額の投資が必要
■オーガニック原材料の安定調達が困難
天候や市場価格の変動による影響を受けやすく、安定した供給体制の構築が必要
■生産コストが高く、利益確保が難しい
無添加・無農薬の原材料を使用するため、一般食品に比べて製造コストが高い
そこで、同社はODM企業と提携し、製造を外部委託することで、オーガニック食品市場へのスムーズな参入を目指しました。
解決策
同社では以下の流れでODM企業と連携し、オーガニックグラノーラの開発・市場投入を成功させました。
1.ODM企業の選定
- オーガニックJAS認証を取得済みの食品製造ODM企業を複数リストアップ
- 原材料調達力、製造能力、品質管理体制を比較し、最適なODMパートナーを決定
2.商品開発と試作プロセス
- 同社が商品コンセプトを設計し、ODM企業と共同でレシピ開発を実施
- 風味・食感・栄養バランスを調整し、消費者ニーズに合った試作品を開発
3.量産体制の確立
- ODM企業の既存設備を活用し、大量生産をスムーズに実施
- 品質管理の基準を確立し、オーガニック認証基準を維持しながら安定供給
4.ブランディングと市場投入
- 同社のブランド名で商品を展開し、オーガニック専門ECサイトや百貨店などへ販路拡大
- ODMを活用したコスト削減により、競争力のある価格設定を実現
【ケーススタディ4】金属加工業界:特殊鋼のODM製造
金属加工業界では、高強度・耐久性・耐熱性を備えた特殊鋼の需要が高まっています。
特に、自動車、航空宇宙、建築、電子機器などの産業では、軽量化や耐腐食性の向上を目的として、より高性能な合金が求められています。
しかし、特殊鋼の開発には以下のような課題があります。
- 高度な製造技術が必要:合金の成分調整や熱処理プロセスには、長年の技術蓄積が必要であり、新規参入のハードルが高い
- 専用設備の投資コストが高い:特殊鋼の製造には専用の溶解炉や鍛造機が必要で、設備投資が莫大
- 品質管理が難しい:製品ごとに求められる特性が異なるため、一貫した品質管理が求められる
そこで、特殊鋼の製造をODM(受託開発)企業に委託することで、これらの課題を解決しながら、高品質な製品を市場投入する企業が増えています。
課題
ある金属加工メーカーでは、航空宇宙産業向けの高耐熱特殊鋼の開発を計画していました。
しかし、以下の課題がありました。
■自社に特殊鋼製造のノウハウがない
一般的な金属加工の技術はあるが、高温環境で使用できる合金の製造経験がない
■専用設備への投資が莫大
特殊鋼の製造には高度な溶解炉や精密鍛造機が必要で、新規導入には多額のコストがかかる
■品質管理が厳しく、規格適合が必要
航空宇宙産業向けの材料は、JIS(日本工業規格)やISO、ASTM規格などの厳格な品質基準を満たす必要がある
これらの課題を解決するために、同社は特殊鋼の製造をODM企業に委託することを決定しました。
解決策
同社では以下のプロセスでODM企業と協業し、特殊鋼の市場投入を実現しました。
1.ODM企業の選定
- 特殊鋼の製造実績を持つODM企業をリストアップし、技術力・生産能力・品質管理の観点から比較
- 航空宇宙向け合金の製造経験があり、ISO 9001、JIS Q 9100認証を取得しているODM企業を選定
2.開発と試作の共同作業
- 同社が求める合金の性能を定義し、ODM企業と試作開発を実施
- 耐熱試験、強度試験、加工性評価を繰り返し、最適な成分配合を決定
3.量産体制の確立
- ODM企業の設備を活用し、大規模な生産ラインを確立
- 品質管理プロセスを強化し、航空宇宙業界の認証基準をクリア
4.市場投入と拡販戦略
- ODM企業で生産した特殊鋼を同社ブランドで販売し、航空機メーカーや部品製造企業と取引を開始
- 高い品質と安定供給を実現し、業界内での信頼を獲得
【ケーススタディ5】電機業界:家電ブランドのODM活用
電機業界、特に家電市場では、技術革新のスピードが速く、競争が激化しています。
スマート家電の普及や省エネ性能の向上が求められる中、新規ブランドが市場に参入するには以下のような課題が存在します。
- 技術開発コストの増加:AI・IoT機能を搭載した家電の開発には高度な技術力が求められ、開発コストが膨大
- 設備投資の負担:新規家電の製造には、大規模な生産ラインや精密な品質管理が必要で、多額の設備投資が必要
- 市場投入スピードの要求:市場競争が激しいため、迅速な開発と生産体制の確立が不可欠
これらの課題を解決するために、多くの家電ブランドがODM(受託開発)を活用し、専門メーカーと提携して開発・生産を進めています。
課題
ある家電メーカーでは、新たにスマート加湿器の市場投入を計画しました。
しかし、以下のような課題を抱えていました。
■IoT技術の開発リソースが不足
スマホ連携や音声制御機能を搭載するには、専用のソフトウェア開発が必要
■生産ラインの新規導入が困難
自社工場では既存の家電製品しか生産しておらず、スマート家電向けの組立ラインを新設するには莫大なコストが発生
■市場投入のスピードが重要
競争の激しい家電市場では、トレンドに乗るために迅速な製品開発と市場投入が求められる
こうした背景から、同社はODM企業と提携し、開発・生産を外部委託することで、スマート家電市場にスムーズに参入することを決定しました。
解決策
同社では以下のプロセスでODM企業と協業し、スマート加湿器の開発を成功させました。
1.ODM企業の選定
- IoT家電の製造実績があるODM企業をリストアップし、技術力・コスト・生産能力を比較
- スマホアプリ開発チームを保有し、無線通信技術に強みを持つODMメーカーと契約
2.試作と開発の共同作業
- 同社が市場ニーズを分析し、ODM企業と共同で仕様を決定
- AI機能付き湿度センサーやアプリ連携機能を試作・テストし、ユーザー体験を最適化
3.量産体制の確立
- ODM企業の自動化生産ラインを活用し、高品質な量産体制を構築
- ODM側の品質管理基準を導入し、製品の安全性を確保
4.市場投入とブランド戦略
- 同社ブランドのスマート加湿器として市場投入
- ODMを活用した低コスト生産により、競争力のある価格設定を実現
【ケーススタディ6】自動車業界:EV部品のODM製造
近年、自動車業界では電気自動車(EV)市場が急速に拡大しており、各国の環境規制強化や消費者のエコ意識の高まりを背景に、多くのメーカーがEV関連技術の開発を進めています。
その中でも、EVバッテリー・電動モーター・充電システムといった主要部品の開発・生産が市場競争の鍵となっています。
しかし、EV部品の開発・生産には以下のような課題が存在します。
- 技術革新のスピードが速く、開発負担が大きい
- 高性能バッテリーやモーター技術の進化により、短期間で新製品を開発し続ける必要がある
- 設備投資の負担が大きい
- EV向け部品の生産には専用の生産設備が必要で、既存の内燃機関用部品工場では対応が難しい
- 品質基準の厳格化
- 自動車業界の品質基準(ISO 26262、IATF 16949 など)を満たす生産体制が必要
このような課題を解決するため、EV部品の開発・製造をODM(受託開発)企業に委託する動きが広がっています。
課題
自動車部品メーカー「同社」は、新規にEV市場へ参入するため、高性能なバッテリーシステムの開発・量産を計画しました。しかし、以下のような課題を抱えていました。
■自社にEVバッテリー開発の専門技術が不足
内燃機関向けの部品製造がメインで、EV向けのバッテリー技術のノウハウがない
■新たな製造設備の導入コストが高い
バッテリーセルの製造には高度なクリーンルーム環境が必要で、大規模な設備投資が必要
■開発スピードを加速させたい
EV市場は成長スピードが速く、競争力を維持するために早急な製品開発が求められる
そこで、同社はODM企業と提携し、バッテリーシステムの開発・製造を委託することで、EV市場へのスムーズな参入を目指しました。
解決策
同社では以下のプロセスでODM企業と協業し、EVバッテリーの開発・生産を成功させました。
1.ODM企業の選定
- EVバッテリー製造の実績を持つODM企業をリストアップし、技術力・コスト・生産能力を比較
- 自動車業界の品質基準(IATF 16949)に適合し、リチウムイオンバッテリーの量産経験を持つODM企業と提携
2.試作と開発の共同作業
- 同社が求める仕様(高エネルギー密度、長寿命、安全性向上)を定義し、ODM企業と試作開発を実施
- 充放電テスト・耐久試験・衝撃試験を繰り返し、EV市場の要求を満たす製品を開発
3.量産体制の確立
- ODM企業の自動化生産ラインを活用し、高品質な量産体制を構築
- 品質保証プロセスを強化し、ISO 26262(機能安全規格)に準拠した製品を生産
4.市場投入と販売戦略
- 同社ブランドのEVバッテリーとして市場投入し、国内外の自動車メーカー向けに販売
- ODMの活用により、競争力のある価格設定を実現
【ケーススタディ7】繊維業界:高機能繊維のODM
繊維業界では、消費者のニーズの変化に伴い、高機能繊維(耐熱性・防水性・抗菌性・軽量性) への需要が高まっています。
特に、スポーツウェア、アウトドア用品、医療用テキスタイルなどの市場では、高付加価値製品が求められています。
しかし、高機能繊維の開発・生産には以下のような課題があります。
- 専門的な技術と研究開発コストが必要
- 繊維の特性を向上させるための研究開発には、長期間のテストと多額の投資が必要
- 新たな生産設備が必要
- 撥水加工や抗菌加工、ナノテクノロジーを活用した繊維製造には、特殊な生産設備が必要
- 市場投入のスピードが求められる
- 急速に変化する市場のトレンドに対応するため、開発・製造のスピードアップが求められる
こうした背景から、ODM(受託開発)を活用し、専門的な技術を持つ企業と提携することで、スムーズに高機能繊維市場へ参入する動きが広がっています。
課題
ある繊維メーカーでは、軽量かつ高耐久性を備えたアウトドアウェア向けの高機能繊維の開発を計画していました。
しかし、以下のような課題がありました。
■高機能繊維の開発ノウハウが不足
一般的なポリエステルやナイロンの加工は可能だが、耐水・耐摩耗・透湿性を兼ね備えた繊維の開発経験がない
■生産設備の新規導入が困難
ナノ撥水加工や特殊コーティング処理には専用の設備が必要で、導入には多額のコストがかかる
■市場投入のスピードを上げたい
競争が激化するアウトドア市場において、短期間で製品を開発し、ブランド企業と契約を結ぶ必要がある
そこで、同社はODM企業と提携し、高機能繊維の開発・製造を委託することで、迅速な市場参入を目指しました。
解決策
同社では以下のプロセスでODM企業と協業し、高機能繊維の市場投入を実現しました。
1.ODM企業の選定
- 高機能繊維の製造実績を持つODM企業をリストアップし、技術力・生産能力・コストを比較
- 耐水性と透湿性に優れたアウトドア向け素材を開発しているODMメーカーと提携
2.試作と開発の共同作業
- 同社が求める繊維の特性(軽量・耐水・耐摩耗)を定義し、ODM企業と共同で試作開発を実施
- 撥水加工・紫外線カット・抗菌機能を備えた複合繊維の試作品をテスト
3.量産体制の確立
- ODM企業の生産設備を活用し、大量生産ラインを確立
- ISO 14001(環境マネジメントシステム)認証を取得した工場で生産し、環境配慮型の製品としてブランド化
4.市場投入と販路開拓
- 同社ブランドの高機能繊維としてアウトドアブランドやスポーツアパレル企業と契約を締結
- ODMを活用した低コスト生産により、価格競争力を確保
【ケーススタディ8】ゴム・プラスチック業界:耐熱素材のODM開発
ゴム・プラスチック業界では、耐熱性・耐薬品性・耐摩耗性に優れた高機能素材の需要が急増しています。
特に、自動車・航空宇宙・医療・電子機器業界では、過酷な環境下でも性能を維持できる耐熱素材が不可欠です。
しかし、耐熱ゴム・プラスチックの開発・製造には以下のような課題があります。
- 高い技術開発力が必要:耐熱性を向上させるためには、特殊な樹脂やゴム配合技術、加工プロセスの最適化が必要
- 専用の生産設備が必要:耐熱素材の製造には、高温成形機・耐熱試験装置などの特殊な設備が求められる
- 品質管理の厳格化:自動車部品や医療機器向けの製品は、ISO 9001・IATF 16949・FDA規格などの厳しい品質基準を満たす必要がある
こうした課題を解決するため、ODM(受託開発)を活用し、専門メーカーと協業する企業が増えています。
課題
あるゴム・プラスチックメーカーでは、電気自動車(EV)向けの耐熱プラスチックカバーを開発することを決定しました。
しかし、以下の課題に直面しました。
■耐熱プラスチックの開発経験が不足
一般的なゴム・プラスチック製造のノウハウはあるが、高温環境に耐える特殊素材の配合技術がない
■生産設備の導入コストが高額
耐熱樹脂成形には高温射出成形機や特殊金型が必要で、新たな設備投資には数億円単位のコストがかかる
■市場投入スピードの確保が必要
EV市場は急成長しており、競合に先駆けて新製品を市場投入する必要がある
こうした状況を打開するため、同社はODM企業と提携し、開発・生産を外部委託することを決定しました。
解決策
同社では以下のステップでODM企業と協業し、高性能な耐熱プラスチック製品の市場投入を成功させました。
1.ODM企業の選定
- 耐熱プラスチックの製造実績を持つODM企業をリストアップし、技術力・品質管理・コストを比較
- ISO 9001・IATF 16949認証を取得しているODMメーカーと契約
2.試作と開発の共同作業
- 同社が要求する耐熱性能(300℃以上の耐熱性、軽量化、高耐久性)を定義し、ODM企業と試作開発を実施
- 耐熱テスト・強度試験・耐候性試験を実施し、EV市場の要求を満たす製品を開発
3.量産体制の確立
- ODM企業の自動化生産ラインを活用し、高品質な量産体制を構築
- 品質保証プロセスを強化し、国際規格に準拠した製品を安定供給
4.市場投入と拡販戦略
- 同社ブランドの耐熱プラスチックとして市場投入し、自動車メーカーと契約を締結
- ODMを活用したコスト削減により、価格競争力を確保
【ケーススタディ9】医療機器業界:ODMによる高精度医療機器の製造
医療機器業界では、高精度・高品質が求められる製品の開発・製造が急務となっています。
特に、画像診断機器や手術支援ロボット、体外診断機器などは、精密な技術と高度な品質管理が不可欠です。
しかし、医療機器の開発・生産には以下のような課題があります。
- 厳格な規制と認証の取得が必要:医療機器はISO 13485・FDA(米国食品医薬品局)・CEマーク(欧州規格)などの認証が必須
- 研究開発コストと時間の負担が大きい:高精度な医療機器の開発には数年単位の研究開発期間と多額の投資が必要
- 高度な製造技術とクリーンルーム環境が必要:精密加工・レーザー技術・無菌環境が求められ、自社設備では対応が難しい
こうした背景から、ODM(受託開発)を活用し、専門メーカーと協業することで、迅速に高品質な医療機器を市場投入する企業が増えています。
課題
ある医療機器メーカーでは、迅速かつ高精度に血液検査が可能な分析装置の開発を計画しました。
しかし、以下のような課題がありました。
■高度なセンサー技術と分析アルゴリズムの開発が必要
血液成分をリアルタイムで分析できる高精度センサーの開発が必須
■認証取得のプロセスが複雑
医療機器認証(ISO 13485、PMDA承認)を取得するための専門知識が不足
■高精度な製造プロセスとクリーンルーム環境が必要
微細加工や滅菌処理が必須で、自社設備では対応が難しい
このような課題を解決するため、同社はODM企業と提携し、医療機器の開発・生産を外部委託することを決定しました。
解決策
同社では以下のプロセスでODM企業と協業し、新型血液分析装置の市場投入を実現しました。
1.ODM企業の選定
- 医療機器の製造実績があり、ISO 13485認証を取得しているODM企業をリストアップ
- 精密センサー技術とクリーンルーム環境を完備したODMメーカーと契約
2.試作と開発の共同作業
- 同社が求める装置の性能(分析精度・処理速度・使いやすさ)を定義し、ODM企業と共同で試作開発
- 生体センサー技術とAIアルゴリズムを組み合わせた試作品を作成
3.量産体制の確立
- ODM企業のクリーンルームで高精度製造を実施し、品質管理を強化
- ISO 13485に準拠した生産プロセスを導入し、安定供給体制を確立
4.市場投入と販路開拓
- 同社ブランドの血液分析装置として、病院・研究機関向けに販売
- ODMを活用したコスト削減により、競争力のある価格設定を実現
【ケーススタディ10】資源・エネルギー業界:環境対応製品のODM開発
資源・エネルギー業界では、カーボンニュートラルやサステナブルなエネルギー活用が世界的な課題となっています。
特に、太陽光発電・風力発電・蓄電池・水素燃料技術などの分野では、環境負荷を低減する革新的な製品開発が求められています。
しかし、環境対応製品の開発・製造には以下のような課題があります。
- 新素材・新技術の研究開発コストが高い:省エネ性能や耐久性を向上させるための技術開発には、多額の投資が必要
- 特殊な製造設備が求められる:リチウムイオン電池や水素燃料電池などの製造には、高度な生産ラインと品質管理が必要
- 環境規制への適合が不可欠:各国の環境基準(ISO 14001、RoHS指令、REACH規制など)に準拠する必要がある
こうした背景から、ODM(受託開発)を活用し、専門メーカーと提携することで、効率的に環境対応製品を市場投入する動きが広がっています。
課題
あるエネルギー関連メーカーでは、高効率で長寿命のリチウムイオン蓄電池を開発し、再生可能エネルギー向けの製品ラインナップを強化する計画を立てていました。
しかし、以下のような課題がありました。
■最新のバッテリー技術の開発ノウハウが不足
エネルギー密度を高め、寿命を延ばすための研究開発が必要
■新たな生産設備の導入コストが高い
バッテリー製造にはクリーンルーム環境や特殊な製造プロセスが求められる
■市場投入のスピードを確保する必要がある
EV市場や再生可能エネルギー市場の成長に対応するため、短期間での製品化が必要
これらの課題を解決するため、同社はODM企業と提携し、リチウムイオン蓄電池の開発・製造を委託することを決定しました。
解決策
同社では以下のプロセスでODM企業と協業し、環境対応型リチウムイオン蓄電池の市場投入を成功させました。
1.ODM企業の選定
- バッテリー製造の実績があり、ISO 14001認証を取得しているODM企業をリストアップ
- 高エネルギー密度と安全性を両立する技術を持つODMメーカーと契約
2.試作と開発の共同作業
- 同社が求める蓄電池の性能(高エネルギー密度・急速充電・安全性向上)を定義し、ODM企業と試作開発を実施
- 充放電試験・耐久試験・安全性評価を実施し、環境基準をクリア
3.量産体制の確立
- ODM企業の最先端生産ラインを活用し、高品質な量産体制を構築
- 環境規制(RoHS、REACH)に適合した生産体制を確立
4.市場投入と販路開拓
- 同社ブランドの蓄電池として市場投入し、EVメーカー・再生可能エネルギー企業向けに販売
- ODMを活用したコスト削減により、競争力のある価格設定を実現
まとめ
ODM(受託開発)は、単なる外部委託ではなく、自社の成長を加速させる強力なビジネス戦略です。
特に中小企業にとっては、技術力や生産力の不足を補いながら、短期間で市場に適応するための最適な手段となります。
受託開発(ODM)は、コスト削減・開発期間短縮・技術力向上など、多くのメリットをもたらします。
自社の強みを生かしつつ、ODMパートナーとの適切な協業を行うことで、競争力のある製品開発が可能になります。
ODMを戦略的に活用し、自社の成長を加速させるための一歩を踏み出しましょう。